High Performance Electrical Connectors
JACO Machine Works excels in machining critical components for high-performance electrical connectors, including those for high voltage applications and interconnectors. Whether for aerospace or telecommunications, we leverage our machining and material expertise to produce top-quality components for the emerging green economy. Our advanced CNC machines and laser welding equipment ensure exceptional precision and consistency, while rigorous quality control processes guarantee each component meets stringent industry standards.
Components we make:
- Fork Connectors - Fork connectors are used in high-performance electrical applications to connect busbars, providing a compact and high-current density connection. They are ideal for blind mating in modular industrial equipment, ensuring reliable power transmission with minimal user interaction. These connectors utilize MULTILAM contact technology for low contact resistance and long service life.
- Sockets and Plugs – These components are used in high-current connectors, signal contacts, and various voltage installations, including machinery and power supplies. Made from brass, copper, and aluminum with silver plating, they feature high current capacity, low contact resistance due to MULTILAM technology, and are available in various standard diameters.
- Modular Connectors – These components are used in high-performance and durable applications like testing, healthcare, and drones, providing connections for power, signal, data, and pneumatic couplings. Made from PEEK plastic, they offer high-temperature resistance and mechanical strength, with up to 100,000 mating cycles, customizable options, and availability in housing or panel mounting.
- Single and Double Fork Plugs for Busbars – These components are used to connect busbars of varying thicknesses, making them ideal for high-current connections in power supplies, energy storage, and converters. Generally made from aluminum and silver-plated, they feature high power capacity, tolerance for angular misalignment, and low contact resistance due to MULTILAM technology.
Machining and Laser Welding Services
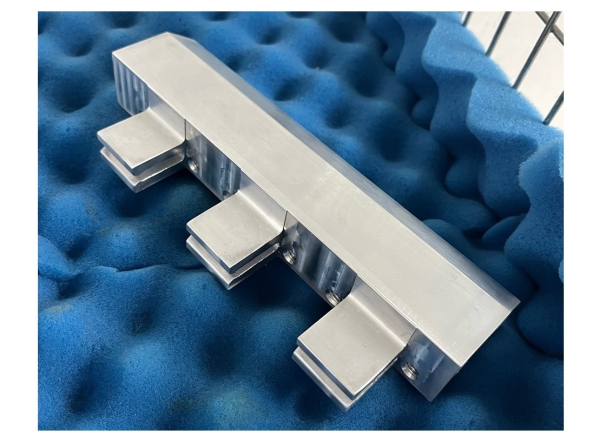
5-Axis Precision Machining – 5 Axis Precision Milling enables the creation of complex geometries essential to make components for high-performance electrical connectors. It allows for machining intricate shapes and angles that traditional 3-axis milling can’t achieve, making it ideal for producing precise components like modular and fork connectors.
Vertical and Horizontal CNC Milling - Vertical and Horizontal CNC Milling machines are versatile, handling various materials and sizes. Both can machine the intricate features of single and double fork plugs for busbars. Vertical CNC milling excels in precision tasks, while horizontal CNC milling is ideal for larger parts, making it suitable for components such as robust interconnectors and high voltage connectors.
CNC and Swiss Screw Machining - Screw Machining is highly efficient for producing small, intricate parts with high precision. Swiss screw machines are particularly adept at manufacturing components with tight tolerances and complex shapes, such as the fine threads and detailed features found in high-performance electrical connectors like sockets and plugs. These machines are essential for producing reliable and consistent parts in large quantities, ensuring that each connector meets the stringent requirements of high voltage applications.
Laser Welding - Laser Welding provides strong, clean welds crucial for the structural integrity and electrical performance of connectors. It’s used to assemble parts like fork and modular connectors, ensuring robust connections for high voltage loads. Its precision minimizes heat-affected zones, preserving material properties and longevity.
Quality Assurance
JACO Machine Works’ comprehensive Quality Management System (QMS) is certified to ISO9001:2015 and AS9100D standards. This certification underscores our commitment to safety, reliability, and precision in every component we produce. Whether it’s risk analysis, raw material inspection, recordkeeping, supplier management, or final assembly, we adhere to strict quality control measures. Here’s how our QMS ensures reliable and repeatable results:
- Continuous Improvement: We evaluate process effectiveness continually. Factors like on-time deliveries, customer satisfaction, and quality conformance drive our improvement efforts.
- Risk Analysis: Identifying and mitigating risks preemptively is essential. Our upper management reviews high-risk jobs before production begins, ensuring quality from the outset.
- Traceability and Documentation: We maintain full lot and material traceability throughout production, complying with customer and regulatory specifications. Rigorous documentation ensures complete accountability and demonstrates product conformance.
- State-of-the-Art Inspection: Our automatic CMM (Coordinate Measuring Machine) uses powerful software to inspect complex part geometries directly from solid model files. This technology allows for fast, repetitive inspections at a low cost.
Why Choose JACO?
JACO Machine Works is a leading CNC machining manufacturer of precision components for many industries, including components for medical devices and surgical instruments, aerospace and defense projects, sensor devices, robotics, semiconductor components, and more. Whatever your application might be, our engineers at JACO are happy to help bring your product to market in the shortest amount of time and at the lowest cost possible. We are committed to providing you with quality engineering, design services, and supply chain management that will exceed your expectations and meet every specification.
Contact us or Request a Quote today to discuss your next project!